About Inmed LLC
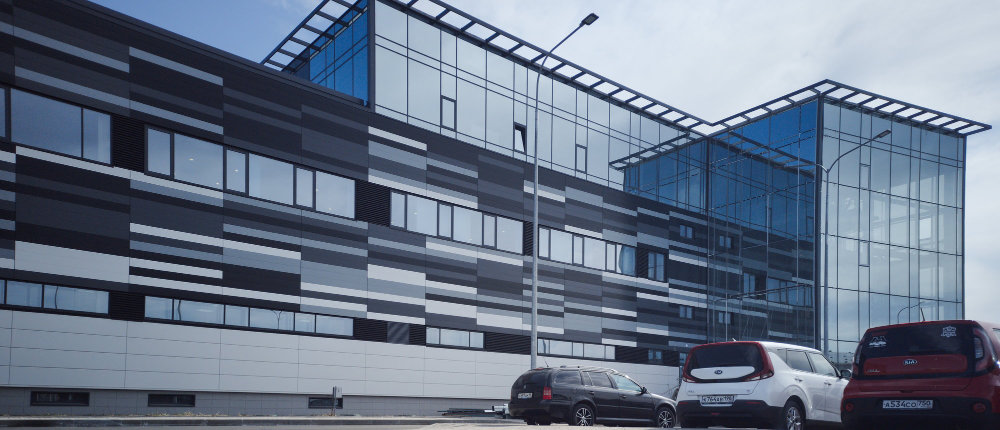
Our Profile
Electrospinning
Our specialization is in electrospinning technology. We develop and produce nanofiber materials for various applications.
“Electrospinning” is a process of formation nanofibers. The term “nanofiber” means literally a thread or filament from tens nanometers to one micrometer in diameter. For comparison, human hair is thicker than nanofiber more than 100 times. First products made by electrospinning were manufactured in the middle of 20th century, but this technology become widespread only in 21sh century as relation to development of chemistry and microelectronics.
There are different types of electrospinning techniques: from polymer solution and from polymer melts. We use the most productive variant – electrospinning from a polymer solution. Organic origin (chitosan, gelatin) and synthetic origin (PVDF, PA, PU) components may be used as polymers. We work with high variety of polymers: chitosan, polyvinylidene fluoride, polyamide, copolyamide, polyurethanes, polyethylene glycol, polylactides, polyglycolides, polycaprolactone, etc.
During the electrospinning process through a strong electrostatic field, nanofibers are stretched into fine filaments, that are randomly formed on the substrate surface. The result of non-woven material presents itself unordered 3D-dimensional structure, looks like a web on photos taken on SEM.
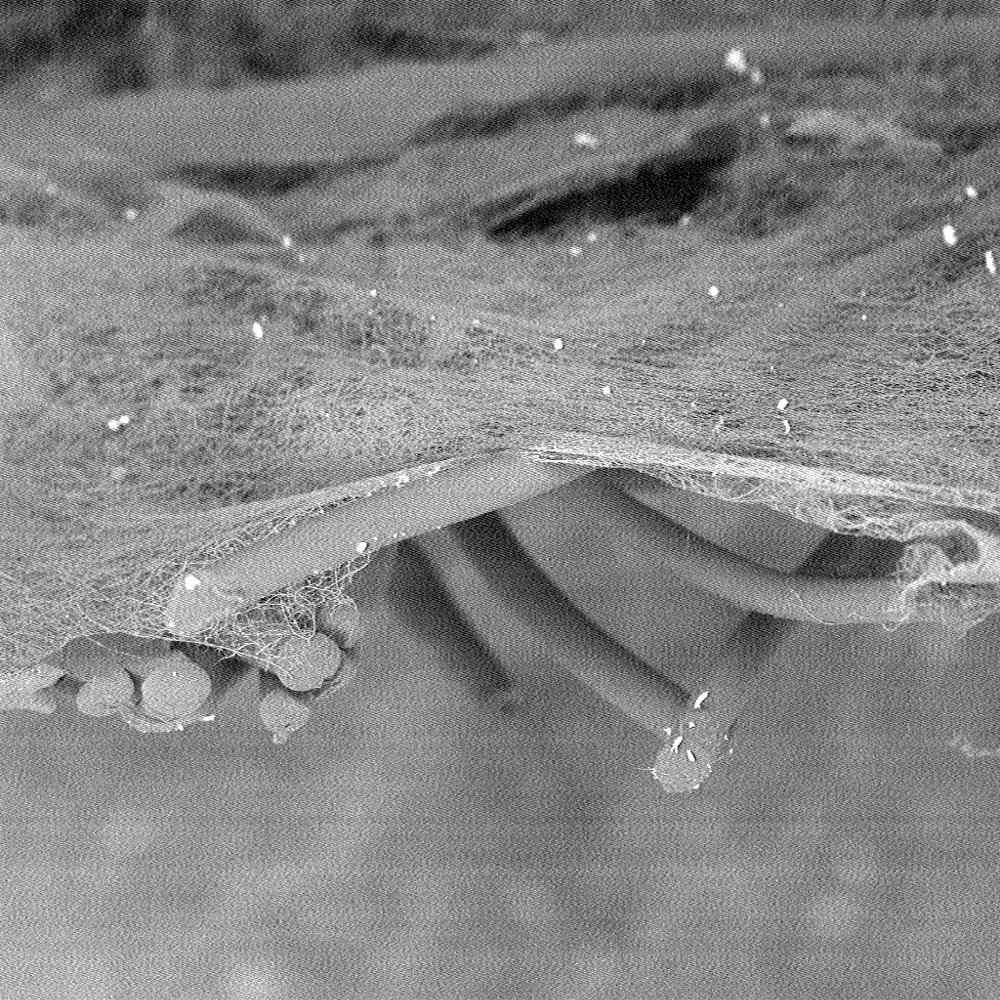

Photos of filtration nanofiber materials taken on a SEM.
Changing solution and formation parameters such as humidity, voltage, viscosity, conductivity, molecular weight, surface tension, etc. allows controlling material structure that determines its properties and application.
Nanofiber applications
Electrospun nanofibers have been successfully applied in various fields, such as nanocatalysis, tissue engineering scaffolds, healthcare, filtration, optical electronics etc.
The most widespread electrospun materials application in filter manufacturing, for example, intake air purification in the gas turbine. The most modern nanofibers application is in the textile industry – to impart functional textiles waterproof, air resistant, and breathable properties.
Company Milestones
2010
Chemical laboratory establishment
Establishing of a chemical laboratory and making a team in Saint-Petersburg.
2012
Synthetic membranes elaboration
Developing of a nanofibrous membrane based on synthetic polymers.
2013
Hemostatic agent development
Developing of a hemostatic agent based on chitosan nanofibers for needs of Ministry of Defence of the Russian Federation. HEMOFLEX® is modern hemostatic gauze for the first emergency aid for temporary control of external arterial, venous or capillary bleeding.
2015
Relocation to SEZ Noydorf.
Establishment of research and production premises in Special Economic Zone Noydorf in Saint-Petersburg, Strelna.
2017
Textile membrane elaboration
Developing of a nanofibrous membrane for waterproof and breathable textiles.
2018
Three-layer textile development
Creating three-layer textile powered by Trivent® membrane, synthetic face fabrics and tricot meshes for waterproof and breathable clothes.